As last weekend’s dramatic season finale in Abu Dhabi demonstrated, motor racing is a seriously technical business. With a need to strike a balance between safety and performance, the design of the car is absolutely crucial. And it’s Rob Smedley’s job to get it right, writes James O'Malley.
Smedley, 48, is Formula 1’s Director of Data Systems, having spent his career working with motorsport big dogs Williams, Ferrari and Jordan, before joining the F1 mothership. He’s spent the last few years working with the FIA, motor racing’s governing body, to write a new rulebook and design a new car for the 2022 racing season.
“The fans have been really clear that they wanted closer racing, they want the cars to be racing wheel-to-wheel,” he explains, “The modern day cars don't allow you to do that, because [though] they generate a lot of downforce, they also generate a really detrimental wake effect. So the flow physics that comes off the back of the car, that's super detrimental for the car behind.”
According to Smedley, a trailing car caught in the wake of another car could lose as much as 40% of its downforce when close behind, creating a potentially dangerous situation as the forces that keep the wheels stuck to the ground are reduced.
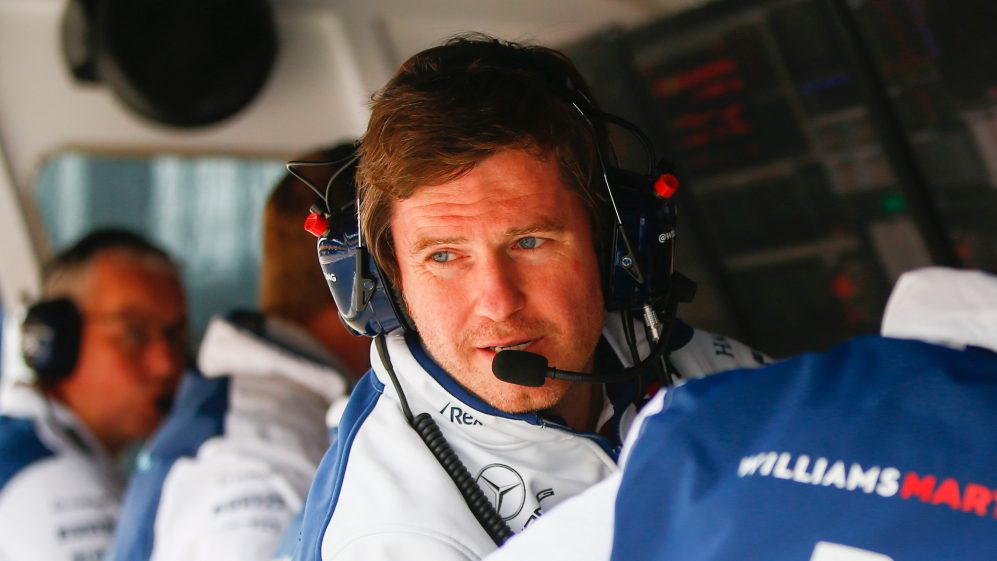
“We had to redesign the architecture, in order to be able to basically [improve] that and come up with something which was significantly less detrimental than the car behind.”
Crunching the numbers using computational fluid dynamics
Traditionally, aerodynamic analysis is performed in a wind tunnel on a 60% scale model of a car, and this still plays a role once the design stage reaches the individual racing teams, but for F1 itself, the first step is to model and iterate designs in a computational fluid dynamics (CFD) simulation.
Smedley explains: “You break your structure down into tiny ‘cells’, and for each cell there's a structural calculation from one cell to the next. So if you put a load into that structure, you get a much more accurate, 3D holistic picture of how that structure deforms or whatever it is that you're looking for.”
Remarkably, this fully digital approach actually provides better data for the design team, as simulations of different material elements can be combined into a single 3D “mesh”.
“You just put all the Navier-Stokes [aerodynamics] equations together, and you just mesh it together, and you get a much more accurate view than the windtunnel gives us on flow physics,” says Smedley.
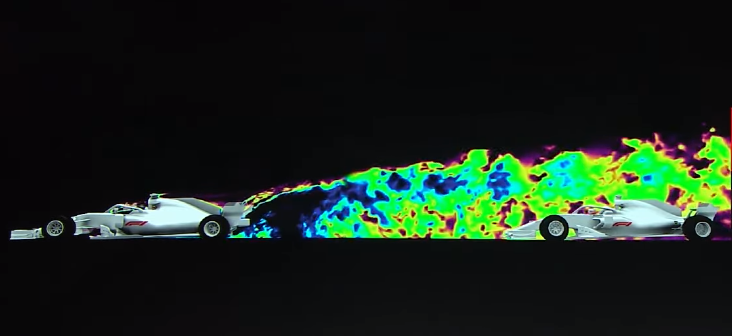
But all of this number crunching is hard to do at speed.
“The compute power was just off the map,” Smedley told The Stack, “Each simulation was taking us an inordinate amount of time.”
The team had access to 550 processor cores in their CFD cluster, and took around 40 hours to run each simulation, which made it hard to iterate at speed.
Follow The Stack on LinkedIn
Though CFD is already widely used in the industry, often with local clusters of computers working together to compute simulations, what made it so time consuming was that Smedley and his team were demanding a much more complex simulation than what is done normally.
“Usually when the teams design their cars within the CFD environment, in order to reduce [compute] power, they take one car, then they split it down the middle, and then they run half a car. So you just rely on the symmetry of the car across the centerline [...] and then you get your results from that.”
In other words, instead of performing the complex maths on 0.5 virtual racing cars, Smedley’s team were computing two entire cars together – one as the lead car, and another trailing, to measure the wake effect.
This is why Smedley turned to the cloud to crunch the numbers. Now his team has the fluid simulation software OpenFOAM running on Amazon’s EC2 servers.
“Using the elasticity of the cloud, it gives us the ability to spin up many more cores, and basically get through the simulations much quicker. So on average, we're up to two and a half thousand cores per design iteration. We went from 40 hours down to seven hours. So the time reduction and efficiency increase was huge.”
“At times, we're running up to 7000 cores, trying to calculate 2.4 billion cells, [computing] 2.4 billion single instances of Navier-Stokes equations.”
The rubber meets the road
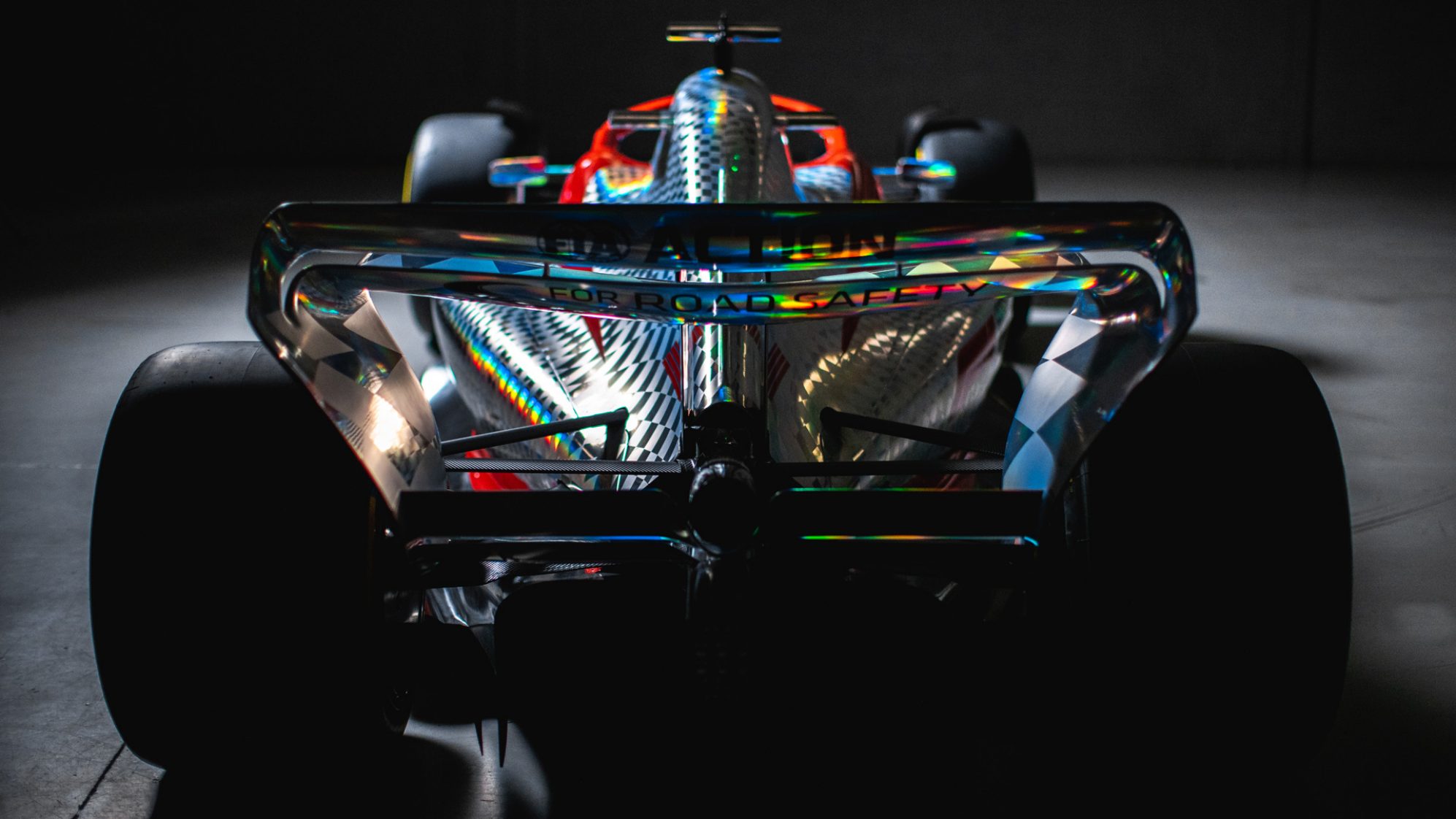
The end result is pretty dramatic, with additions that include new over-wheel winglets and a redesigned front wing, to direct air around rather than under the car. According to F1, the current car loses 35% of its downforce when 20m behind the lead car, which rises to 47% when only 10m away. By contrast, Smedley’s newly redesigned car loses just 4% at 20m, and only 18% at 10m.
So the goal of wheel-to-wheel racing could be in sight. But how can Smedley know if the simulation truly reflects real world conditions?
“You're constantly trying to get correlation between what you're doing in the virtual world, whether that's physically in a wind tunnel, or digitally with it in computational fluid dynamics, and what's happening on the track,” he explains.
“Data is brilliant. Data is the lifeblood of everything that we do as engineers. But it's got to be good data, it's got to be incredibly high quality, either at simulation level or at track acquisition level. It's only then that you can start to understand [if] this is working.”
So though the 2022 design has been finalised, there is still the real world test to go. But this will have to wait until the individual racing teams have finished building their cars to the new specification, and line them up on the starting grid.
“We're not able to collect any track data yet,” says Smedley, “But once we do start collecting track data, it will then be important to use that data to correlate our models and to make sure that our simulations then are more accurate for the next round and next iteration of this design.”
So the process never really ends, as Smedley looks forward to iterating the design even further in the future.
“One of the things about Formula One is that it's constantly evolving,” says Smedley, “If you look at Grand Prix racing in 2021/2022, compared to Grand Prix racing in 1950, when it started, there's hardly anything that's the same. Apart from one thing, which is the culture of excellence, which is that culture of trying to exploit the maximum out of humans and machines.”
So if you thought the race in Abu Dhabi was close then perhaps next year, with improved cars that need not fear each other’s wake… perhaps as the cars speed towards the chequered flag, the race will be even more nail-bitingly close.